What HPLC Operators Need to Know Part 2: Column Selection, Mobile Phase Gradients, and Detectors
During this two part event we will look at the entire HPLC separation process from mobile phase selection and preparation, to injection, separation, and detection, from the perspective of the laboratory practitioner. We will provide practical hints and tips for the essential HPLC parameters in order to make your use of this powerful technique straightforward and successful. In part one we discussed how and why mobile phases are chosen and prepared and the different variations of HPLC pumps and autosamplers which are available. Part two starts with column selection probably one of the most important choices in any chromatographic method. We will share our insights on how to select the correct column each time covering particle size, morphology, physicochemical properties as well as stationary phase selection. Finally, we will detail how to utilize and optimize HPLC gradients and review the various detectors available and when and how they are best employed.
Topics include:
- What are the most important physicochemical parameters of the support material
- What are the differences and relative merits of fully and superficially porous particles and what role does particle size play?
- What are the most common stationary phases available and how do they influence selectivity – when are they best employed?
- Are mobile phase gradients always required?
- How is a gradient formed and what are the most important parameters to control
- How are gradients optimized during method development and effectively transferred from HPLC to UHPLC, or vice versa
- Role and function of (U)HPLC detectors
- Physicochemical analyte properties which influence detector choice
- Working principles of variable wavelength and diode array UV detectors with key operational variables
- Why, when, and how would refractive index (RI), evaporative light scattering (ELSD), fluorescence (FLD) or charged aerosol detectors (CAD) be used?
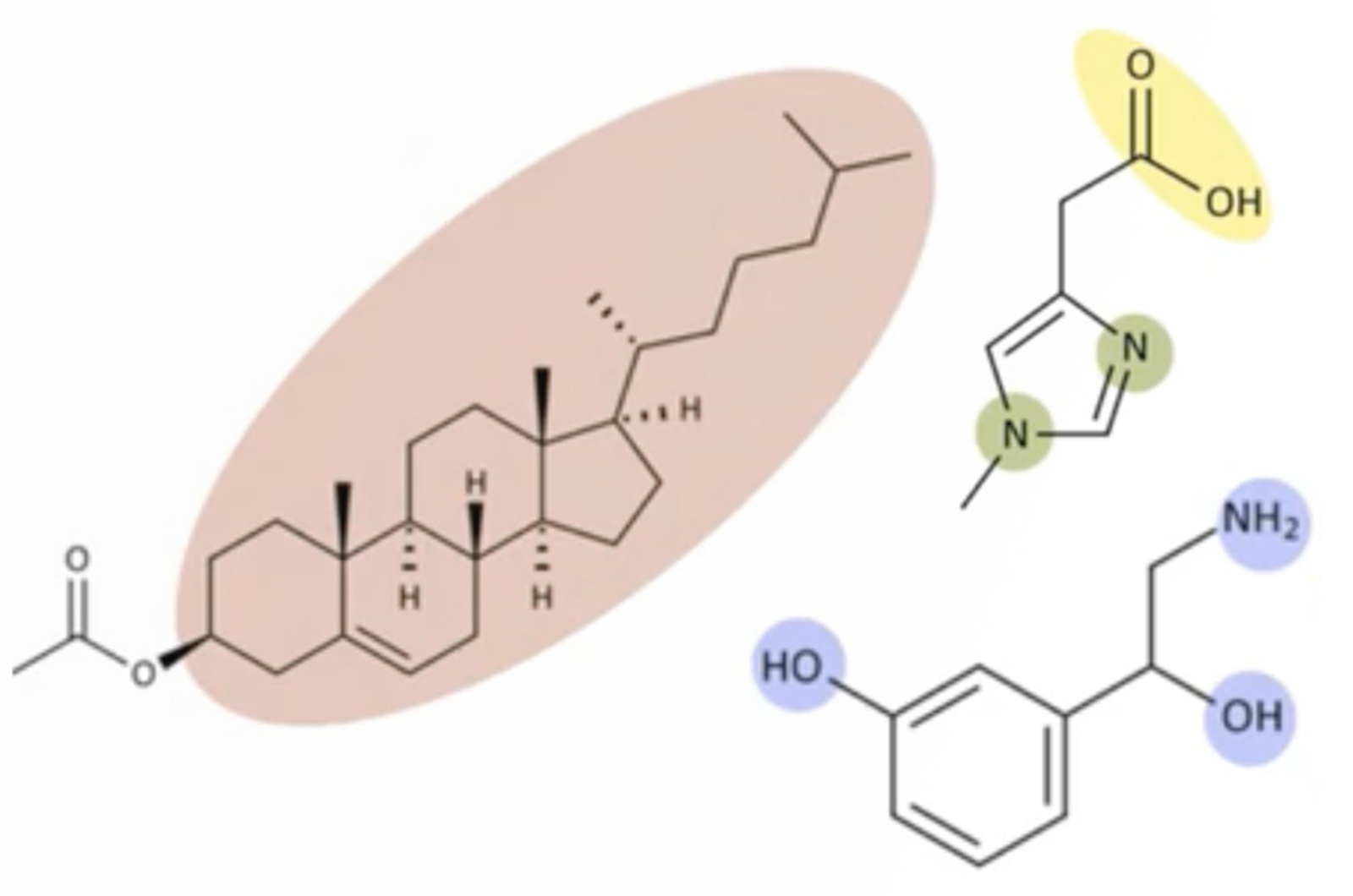